Strategic review to drive reduction in expense ratio for commercial insurers
INTRODUCTION
While COVID-19’s immediate impact on industries such as travel, tourism and hospitality has made itself abundantly obvious, the pandemic has spared no industry or economy. Every sector is challenged; with it’s buoyancy under threat. Businesses are recalibrating in real-time to the changing needs and situations of their customers, workforce and suppliers and at the same time developing strategies to mitigate the financial and operational risks that have surfaced in the wake of these uncertain times.
As part of a heavily regulated field, insurance companies are limited in options when it comes to increasing profit margins outside of investment revenue. Between actuarial table algorithms and insurance restrictions and regulations, premiums pricing is practically fixed, leaving insurers little room to compete on price. Market volatility has caused the yields to flatten across government and non-government bonds, while dropping interest rates cause further pressure on the insurers. With reducing revenue and increasing losses, overall combined ratio has taken a large hit.
Insurance market Lloyd’s of London has said it expects COVID-19-related claims to cost it $3bn to $4.3bn. The losses could rise further with every continued period of lockdown. Global non-life underwriting and investment losses may hit a record approximately $200 billion in 2020. In a double blow, insurers have also lost money due to falling markets, slashing the investments they use to pay out claims.
The priority, therefore, is not just cutting cost. Rather, the question is, where should insurers focus resources to stimulate growth and achieve strategic cost reduction? And what about digital transformation, which can not only sharpen the precision of risk selection and pricing, but also deliver more tailored and targeted client solutions at a fraction of the cost? The situation calls for a strategic review and rationalization of the expense portfolio.
EXPENSE RATIO CONSTITUENTS: WHAT’S THE OUTLOOK FOR INSURERS?
Insurance industry leaders have already identified that some expenses, which were previously seen as necessary evils, are in fact variables that can be altered.
The constituents of the expense ratio can broadly be categorized as:
- Go-to-market expenses (includes new product development, marketing and sales expenses)
- Operations expenses
- IT expenses
- Enabling functions expenses
Of these constituents, operations has always been the major contributor. While in the past decade operations’ contribution towards the overall expense ratio has reduced, our research suggests that it still holds the lion’s share. The remaining constituents share the rest of the pie more or less equally.
However, the coming years will bring a greater focus on reducing administrative costs and the current share of the constituents will shift further. Businesses are looking at new ways to modernize their operations through digitization, automation, consolidation and centralization and offshoring. These can all contribute to lowering the administrative cost base. Our research suggests that the current wave of digital transformation should further reduce operations-focused expenses by approximately 35-40%.
With businesses starting to opt for product distribution through digital platforms and promoting customer self-service, the administrative burden of marketing and sales is also set to reduce. As a result, expenses focused on marketing and sales will drop by 25%. However, the approximately 50% of efficiencies gained from reduced spend on administrative marketing and sales tasks will be utilized in new product development, with an emphasis on speed to market. Overall, go-to-market expenses should reduce by approximately 15%
Focus on process automation, full system integrations, APIs and robust infrastructure will see an increased spend in IT. We estimate that IT spend to support the digital transformations that businesses should increase by approximately 10%.
Businesses are also looking at automating tasks and consolidating and offshoring major aspects of several enabling functions. Some are looking to completely outsource functions such as HR and finance and shift to a Function-as-a-Service model. These measures are here to stay and will reduce spend on enabling functions by around 25%.
EXL’s Research
INTERACTED WITH TOP P&C CLIENTS AND MODELLED THE IMPACT OF EFFICIENCIES THROUGH
- Target Operating Model changes which includes aspects such consolidation/centralization, offshoring, process and technology improvements to name to few
- Business Process Automation and Business Process Re-engineering
COST DRIVERS FOR EXPENSE RATIO CONSTITUENTS
In the current scenario, for an insurer to be profitable it is important to understand the main cost drivers for expense ratio along with the contributing factors and key challenges to overcoming them. We will focus here on key levers contributing to operational cost—operations and Technology/IT, revisit the strategy and zoom in on optimizing operational expenses to maintain competitive edge and maximize the potential for future growth.
OPERATIONS
Operational cost is the largest insurance cost contributor; approximately 40% of the overall expense ratio. Companies are largely focusing on reducing the operational cost as reduction in these costs driver influence increased efficiency, better customer satisfaction, streamlined process which should further enable automation.
Some key factors drive higher operational expense cost:
- Fragmented operations across geographies/units: A sub-optimized, dispersed and non-cohesive operating model combined with complexities arising from aspects such as product-portfolio mix, geography and distribution channels is one of the biggest drivers of cost for an insurance firm. Further, this kind of sub-optimized operating model is often the root cause of insurers failing to leverage economies of scale. High-cost players tend to have a fragmented and sub-optimal operating unit set-up.
- Sub-optimized processes: An inconsistent process that is incorrectly mapped to resources in siloed operations, with a limited cross-product line view, greatly increases admin cost. A sub-optimized operating model is the leading reason for teams needing to manage a number of non-value add activities and large amount of rework in the processes. High-cost players tend not to have consolidated or optimized the setup of their operating units. Optimizing processes has always helped companies to drive efficiency, build scale for automation, reduce dependencies and thereby reduce the overall cost of servicing.
- Reliance on manual processing: Underwriting, claims and finance processes are scattered and low-value transactional processes contribute to wasted costs (in underwriting, for example, up to 80% of sales time is potentially spent on administration). These processes often rely on heavy manual workarounds, including re-keying of information onto multiple systems. Typically, claims and underwriting processing takes several days as insurers gather and check data from multiple sources. It may take even more time, due to human errors such as mismatched financial data or incorrect customer details. Such delays can result in the loss of customers and other financial and reputational damage to the company.
- Resource utilization: In the current scenario, with reduced workforces and remote working operation centers are not running at their usual productivity. Optimizing resource utilization and managing operations through call centers, shared services and payment processing centers are crucial to successfully navigating rising pressure on cost. It is critical for organizations to be fully apprised of the available roles and skillsets and dynamically assign a taskforce to respond to needs as they emerge.
Some particular challenges faced by insurers, as they look to reduce operational cost:
- Business complexity: This refers to the degree of standardization and rationalization that is incorporated across the product portfolio and business processes. Bespoke processes and large product portfolios coupled with myriad of distribution channels tend to cause operational costs to soar. Complexities relate to product mix, process design, process segmentation, location diversity: all are important drivers for operating costs and complexities here limit insurers’ ability to leverage economies of scale.
Although many businesses consider a large product portfolio to be a differentiating factor, introducing variances has an impact on the underlying workflow—the processes that govern operations. With each introduction of variances, staff must be trained and upskilled, which contributes to downtime and falling productivity while driving an uptick in administrative and overhead costs to manage the new variances. - Resource utilization: Capacity management and the ability to deal with peaks in demands and plug in resourcing gaps helps drive efficiency and goes a long way towards retaining customers.
- Regulatory compliance: Insurance companies must comply with a significant number of regulations. Amendments to these regulations often force insurers to reorganize their business processes in order to adapt. Compliance breaches result in financial and operational damages to companies, but the reliance on routine manual operations that are prone to human errors raises the risk of compliance breaches.
TECHNOLOGY/IT
A fragmented legacy IT landscape hampers the ability to harness economies of scale and drives high IT and operational costs. With the current COVID-19 pandemic, society in general is forced to ‘go digital’ and embrace minimized human contact for transactions of all kinds.
Some key factors contributing to high IT expense are:
- Legacy systems: Many insurance companies still rely heavily on legacy apps, programs and systems for managing business operations. These legacy information systems are highly fragmented, leaving businesses unable to fully leverage economies of scale that modern software systems bring to the table. Changing existing systems, of course, requires strategic investment of both money and time. Therefore, businesses often stick with old systems, even though maintaining them is no longer a cost-effective measure.
- Multiple systems to target similar outcomes: A fragmented landscape—particularly where we see too many technology elements, both hardware and software, serving as the platform for business operations—drives IT costs and negatively impacts operational costs, too. Consolidating, rationalizing and improving the technology landscape simplifies business operations, allows the business to benefit from automation by providing scale and positively impacts product development timelines and speed to market.
- Rising Total Cost of Ownership (TCO) due to increased operational and retirement cost: Controlling costs and managing new acquisition expenses have become pivotal goals for companies over the last few years. Forrester estimates that 80% of total IT budget is spent on maintenance, while only 20% is geared towards new projects and initiatives. Aligning IT expenditure with business resources and requirements is a key challenge for enterprises today. An increasingly mobile workforce, complex security requirements for regulatory compliance and longer process lifecycles are some of the factors that have made managing an archaic IT landscape a more complex and demanding task than ever before.
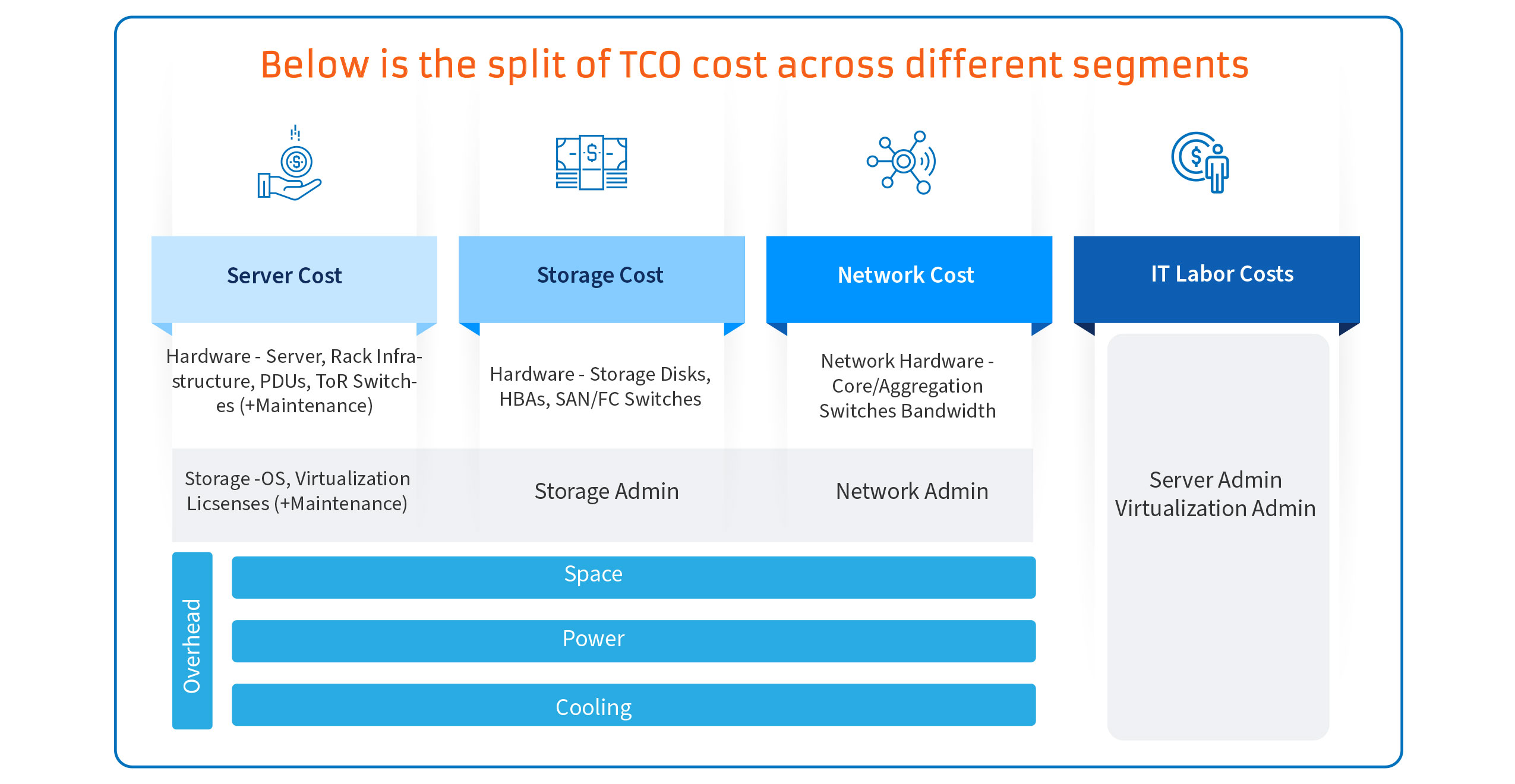
Some of the key challenges faced by insurers in reducing IT expense are:
- Business complexity: Technology change brings varied complexities to the fore, particularly with respect to the regulations and procedures required for business operations, the processes, procedures and services necessary to be competitive and the business organization structure, processes, systems, infrastructure and products.
- Cost of change: Maintenance of multiple systems is one of the largest IT costs in an organization. Change requires large investments of money and time, leading some businesses to stick with legacy and unproductive systems as the path of least resistance.
- Resistance to digital change: In the past, most organizations embarking upon their transformation journey saw digital as a key focus area but encountered significant resistance from both external and internal customers. Customers are not always tech-savvy or eager to give up old ways of engaging. Employees, too, may be resistant to change.
However, in the era of COVID-19, digitization has been forced upon customers and employees. For businesses to counter pressures from competitors and manage deaccelerated revenues, this is the way forward.
As businesses and their customers adapt, automation will play a vital role
How will automation play a role in your organization in the next 12 to 24 months?
(Percent respondents)
LEVERS TO INFLUENCE THE COST DRIVERS AND REDUCE EXPENSE RATIO
Insurance leaders know that the full impact of COVID-19 is still unfolding, but the decisions made today and in near future will determine the future of their organizations. The key priority for businesses in the uncertain present-day scenario must be to focus resources to stimulate growth and strategically reduce costs.
MINIMIZE THE IMPACT OF COVID-19
Most insurers find themselves at this stage, currently. The focus is on protecting employees, safeguarding the core operations function, managing productivity and communicating effectively while ensuring no disruption to customer support and controlling the expense ratio. Best practices for managing expenses across operations and IT are:
OPERATIONS
When it comes to re-defining the future state operating model, businesses cannot rely on a ‘one size fits all’ approach. They must balance customer value, cost-to serve and digital adoption if they are to maximize value while enhancing customer experience. For example:
- Re-prioritization of ongoing initiatives: While innovation is necessary, it is important that all projects are prioritized based on immediate goals.
- Reducing business complexity: Reducing complexity across products and processes with a streamlined IT platform helps drive digital transformation more effectively. Insurers need to understand the details behind their cost levels on a per product, per channel or per location view, for example. This will enable insurers identify the root causes of business complexity and develop targeted countermeasures.
- Enabling remote working and flexible workforce: An effective and efficient environment that enables and supports remote working will allow organizations to significantly reduce real estate costs (an average of $11,000 per year per part-time telecommuter) or generate up to 21% higher profitability.
TECHNOLOGY/IT
- Looking for economies of scale: With greater scale, costs are spread and this contributes to reducing the average unit cost, Enabling functions such as sales and marketing, HR and finance are prime targets for achieving digital economies of scale.
- Managing TCO expenses: Looking at the total cost of ownership is a way of assessing the long-term value of a purchase to a company. Organizations use the total cost of ownership as a means to assess potential purchases and business deals. Two initiatives that are particularly recommended for managing TCO are:
- Cloud computing: Cloud computing is a very efficient way to lower business expenses, by reducing staffing cost, hardware cost and using pay-as-you-go software. Organizations can take advantage of low or no initial setup costs and pay monthly or annually for cloud services based on usage and business need rather than purchasing, deploying and maintaining an IT infrastructure or enterprise software system.
- Business integration: Integrating, automating and optimizing key process will yield large benefits. System integration can help reduce overhead cost and eliminate manual processes. There are various business integration solutions on offer, but businesses should choose the solution that can enable electronic data exchange and data synchronization and eliminate duplication.
ACCELERATE THE CONTROL OF EXPENSES
Now is the time for insurers to zero in on controlling expenses and taking strategic action to optimize the operating model while pushing forward with digital transformation initiatives. Best practices for managing expenses across operations and IT include:
OPERATIONS
Optimizing the operating model is key to cracking the cost issue. This requires a holistic examination of the operating model, including processes, location footprint, supporting technology, employee skills, sourcing, and organization and governance structures. Focus areas include
- Consolidation and outsourcing: This key initiative will contribute towards reducing the unit costs; when applied to activities such as policy issuance, policy administration and handling claims, it leads to reduced effort and optimal utilization of resources. Every future state operating model will differ: one insurer consolidated all existing operating units in one central location to gain economies of scale, while another created six regionalised operating units to establish a location-optimized footprint and maintain proximity to local business units.
- Portfolio rationalization: Offloading unprofitable lines of business or those that are resource-intensive yet generate limited value improves and streamlines the portfolio.
- Build a continuous improvement culture: To reduce costs sustainably, insurers need to embed cost-consciousness and continuous improvement in their business culture. Back office cost can significantly be reduced by promoting a culture where employees are encouraged and rewarded to proactively look at opportunities to improve processes.
- Improve efficiency with workflow automation: Overcoming inconsistencies in the workflow is key to effective digital transformation within any operational process. Below is an example of the process to transform commercial underwriting that we have deployed across clients, which not only helped in reducing expense ratio but also improved customer satisfaction and retention.
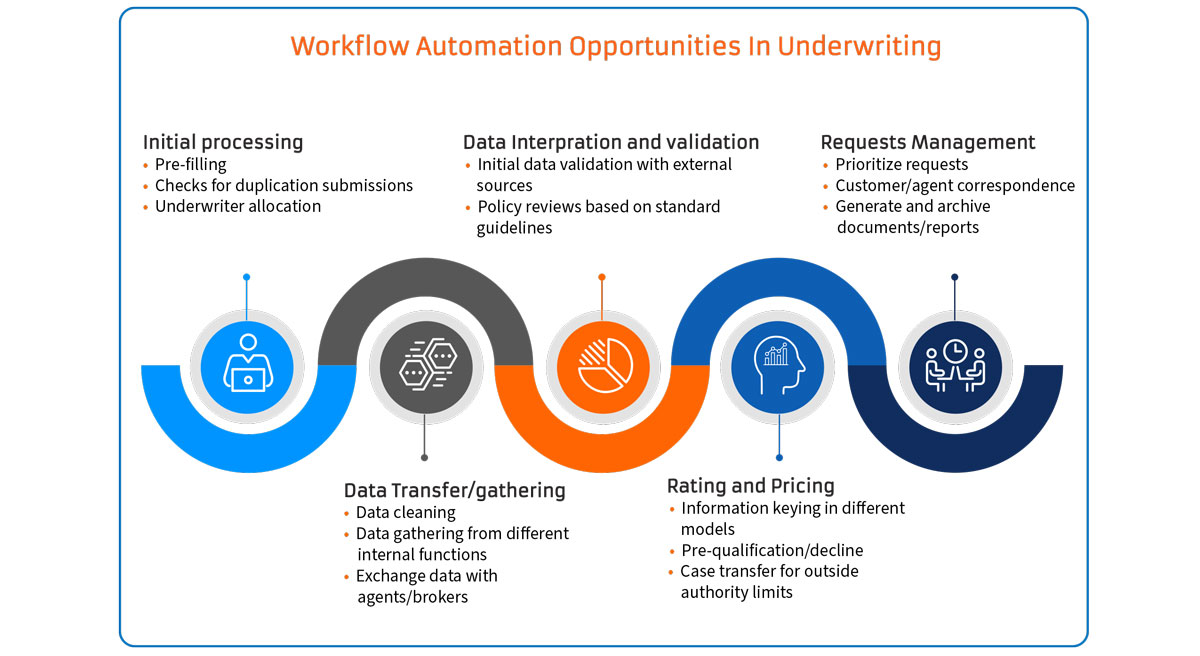
TECHNOLOGY/IT
Some insurers that have pursued digital transformation find themselves stuck in a deadlock, which will have a negative impact on their response to the COVID-19 crisis. As and when the crisis eases, insurers must prioritize investment in digital transformation initiatives. Considerations include:
- While investment will be required in the short-term to digitize operations (back office and internal workflows) and promote digital offerings, this will pay off by significantly reducing maintenance and support costs. Innovation in technology will also reduce the administrative cost burden.
- Digitized distribution, underwriting, processing and claims lowers the fixed costs and creates much-needed scalable business operating models
- Design thinking, a creative approach to problem solving, is invaluable in restructuring business processes with customer outcomes in mind and can be very effectively employed in the insurance field. Design thinking requires crossfunctional teams to examine the end-to-end customer journey, find the moments of truth and map out digital and human interventions.
PLAN FOR FUTURE
Shifting from human-centered to digital processes can help insurers prepare for the future. Below are best practices for managing expenses in a future-focused way across operations and IT:
OPERATIONS
- Sustain performance management: A sustainable performance management approach means simultaneously changing mindsets and behaviors, defining new performance metrics and targets, designing new processes, and establishing performance dialogs – all of which need to cascade between hierarchy levels.
- Embrace evolving technologies: Advances in artificial intelligence and the Internet of Things (IoT) have opened up new markets and new opportunities. Telematics, home sensors, drone surveys and other innovations can provide insurers with critical data they can leverage, using analytics, to make better decisions in areas including underwriting, pricing and claims adjudication. Digital data flows help insurers manage their customers as individuals rather than groups—a core expectation of today’s digital customer.
TECHNOLOGY/IT
We are seeing an acceleration of the digitalization of the insurance factory process. Many insurers have, over the last five years, started to implement true digital capabilities. This activity has usually addressed ‘hot spots’ within the value chain, and this has provided the brokers, and customers with some degree of self-service, however in most instances there is still significant analogue drop off which still needs to be transformed. As the situation stabilizes, companies will be able to accelerate their digital transformation efforts, in collaboration with the right technology partners. This will give them the platform, technology and skills needed to prepare for and face future crises.
- Benefiting from data and analytics across the board: According to McKinsey, leading companies are using data and analytics not only to improve their core operations, but also to launch entirely new business models:
- Some insurtech companies, though at an early stage of their evolution, are utilizing online customer journeys, comparison platforms, chatbots, automated underwriting and claim adjudication, pricing algorithms and peer-to-peer networks for capital deployment.
- Enabling real-time decisions with IoT-generated data streams: Most of the major insurers have started utilizing datadriven analysis and IoT for faster and more accurate analysis and response. This works both for insurers and customers as, based on analyzed data, insurers can offer discounts to customers.
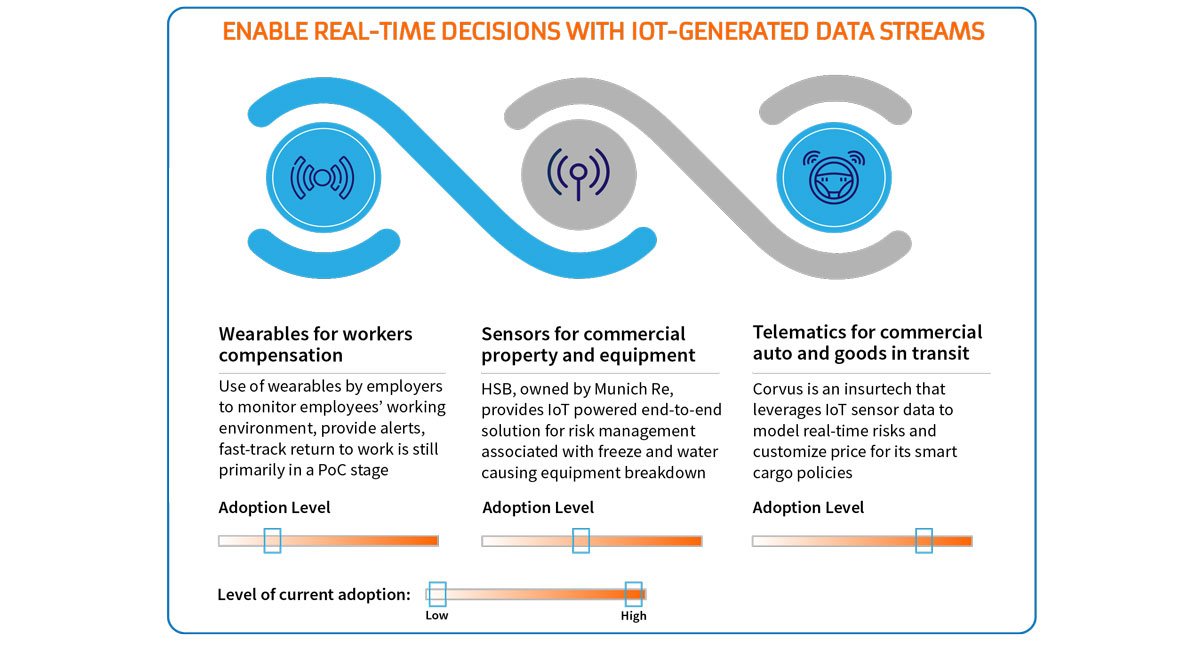
Apply a three-step digital transformation process:
- Standardize and optimize business operations: Simplifying and driving operational efficiency in underlying systems, IT infrastructure and the flow of data through the lifecycle of the operation in question will enable insurers to costs from the current stack. Optimization should always have the overall vision as its North Star and should pave way to introducing advanced technological capabilities.
- Digitize their standardized and optimized processes: Leveraging technologies such as robotic process automation reduces manual labor and enables processes and services to be available anytime, anywhere. Digitization can be accelerated by adopting cloud-based solutions that provide the requisite speed and agility while reducing TCO.
- Augment digital operations using data: Control over data is key to digitally transforming an organization. Thanks to legacy systems, most organizations have valuable data residing in different sites across different systems that do not interact. Considering the strong push to utilize data to understand behavioral economics and customer preferences, effective data management is imperative. An organization’s ability to harness macro and micro insights from predictive and prescriptive analytics, supported by artificial intelligence, will provide it with a strong competitive edge in the future.
When digitalization starts to provide competitive edge and opens up new sources of revenue, or improves the growth of current streams, that is when what began as a cost-cutting exercise transforms into an exercise that drives differentiation and sets an insurance organization apart.
CONCLUSION
Insurers are going to continue to focus on Customer Experience, better outcomes and Cost optimization to determine their operating model for the future. To stay competitive insurers have significant opportunity to thrive with longer term success by strategically reviewing and controlling the expense ratio.
Over the years, EXL has built solutions and frameworks that drive rapid outcomes for insurance firms, helping several large insurers drive rapid transformation to impact the expense ratio. To learn more or explore your options, please visit www.EXLservice.com.
EXL proprietary methodology combines the power of Analytics and Digital with domain relevance and data insights to transform Operating Model and achieve the trifecta of Customer Experience, Business Outcome and Optimisation of Operational Costs
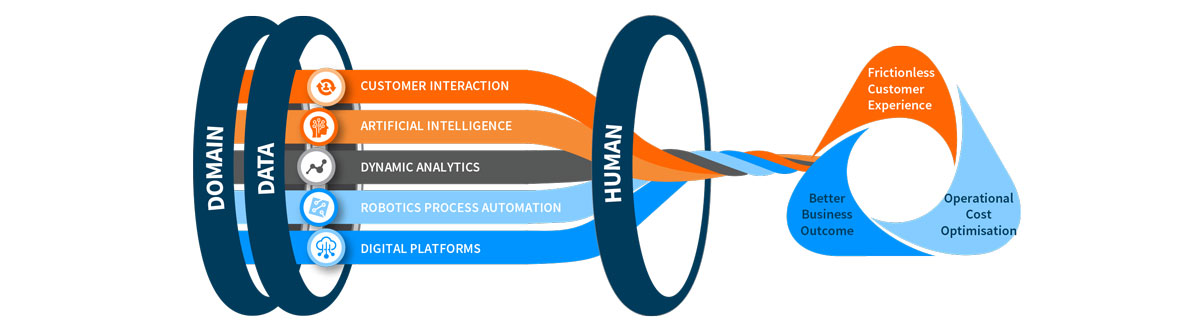
For further details about EXL’s solutions, please feel free to contact the author, Rohan Regis, at rohan.regis@exlservice.com
Sources
- https://www.pwc.com/gx/en/insurance/publications/firing-on-all-cylinders-five-steps-to-strategic-cost-reduction.pdf
- https://www.pwc.co.uk/issues/crisis-and-resilience/covid-19.html
- https://www.strategyand.pwc.com/gx/en/unique-solutions/fit-for-growth/end-to-end-transformation.html
- https://www.finextra.com/blogposting/18626/covid-19--a-booster-for-digital-transformation
- https://assets.kpmg/content/dam/kpmg/ch/pdf/business-at-risk-operations-whitepaper.pdf
- https://medium.com/the-future-of-financial-services/digital-transformations-that-dissipate-costs-d552b736008a
- https://www.the-digital-insurer.com/more-for-less-five-steps-to-strategic-cost-reduction-pwc-whitepaper/
- https://www.mckinsey.com/~/media/McKinsey/Industries/Financial%20Services/Our%20Insights/Time%20for%20insurance%20companies%20to%20face%20digital%20reality/Digital-disruption-in-Insurance.ashx
- https://www.mckinsey.com/~/media/mckinsey/industries/financial%20services/our%20insights/what%20drives%20insurance%20operating%20costs/successfully_reducing_operating_costs.ashx
- https://michaelskenny.com/points-of-view/evaluating-the-total-cost-of-ownership-for-an-on-premise-application-system/
- https://assets.kpmg/content/dam/kpmg/xx/pdf/2019/03/operational-excellence-report-2019.pdf
- https://www.rte.ie/news/business/2020/0514/1138309-lloyds-of-london-claims/
- https://www.forbes.com/sites/laurelfarrer/2020/02/12/top-5-benefits-of-remote-work-for-companies/#4c9a39ca16c8
Author:
Rohan Regis
Director,
Insurance Consulting & Solutions
Rohan.Regis@exlservice.com
Contributors:
Mohit Manchanda
VP and Head of Insurance,
UK & Europe
Mohit.Manchanda@exlservice.com
Sidhartha Sinha
Senior Manager,
Insurance Consulting,
Property and Casualty
sidhartha.sinha@exlservice.com
Sumeet Shetty
Senior Manager,
Insurance Consulting,
Property and Casualty
Sumeet.Shetty@exlservice.com